HANDLOOM
HANDLOOM
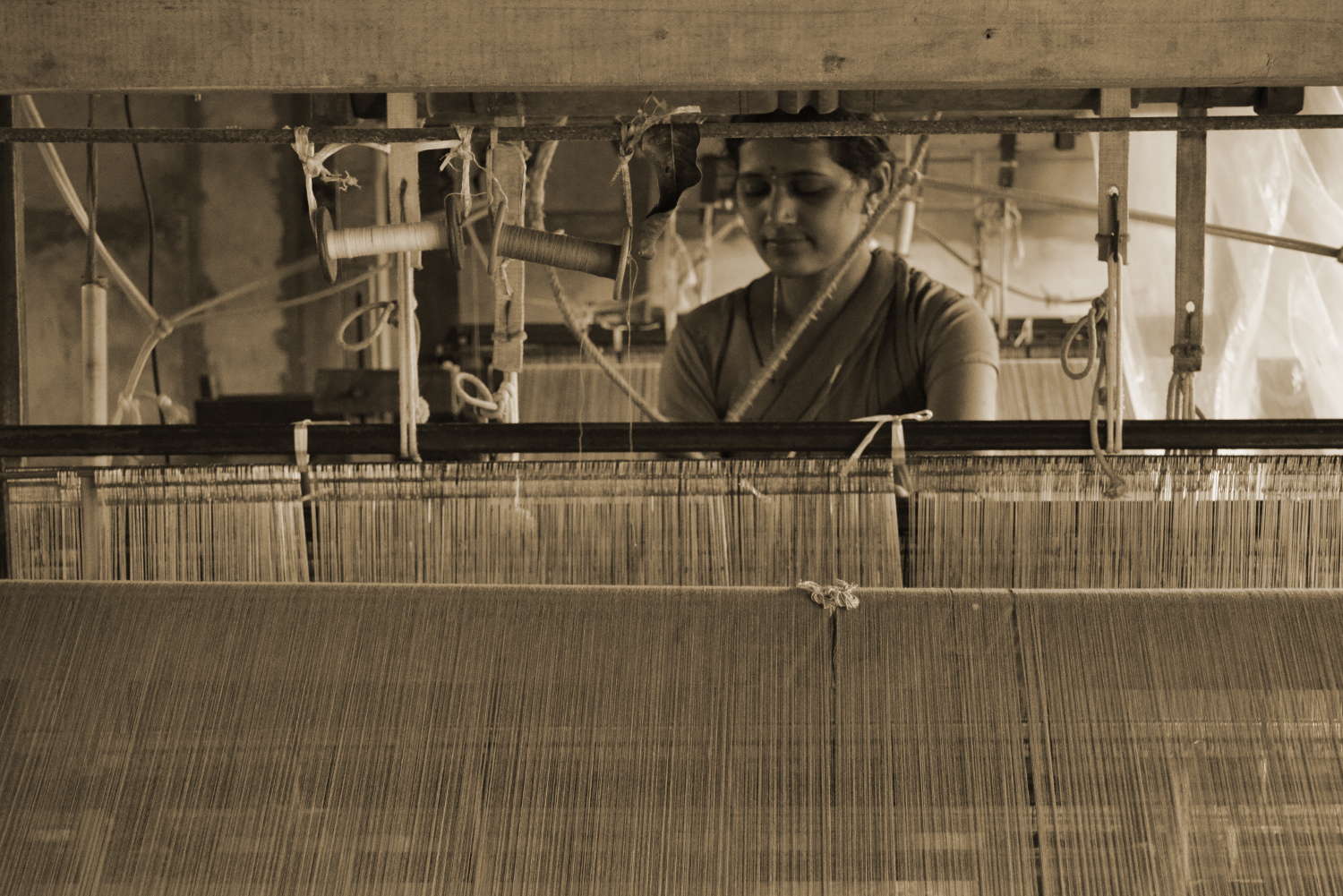
Handloom is the name given to fabric that is woven by a hand-operated weaving machine or “loom”. It is also referred to as “hand woven”. Handloom fabric came into being during 19th century when the British started producing cotton yarn using automatic machines at factories in England and dumping it on our weavers. Our country has a rich tradition of handloom and a variety of fabric, each a specialty of the region of its origin.
World over, there is great demand for handwoven fabric and only India still has handlooms left. Whatever is remaining is soon getting wiped out. There is an urgent need to preserve this and bring back the traditional weavers to their profession.
Handloom provides an alternate income for families by employing the womenfolk who can work from the comfort of their homes. The “looms” can be of various types - pit loom, frame loom etc. depending on the way it is constructed. But the underlying principle is the same.
Handloom, just like Khadi acts as a tool for social change by breaking the caste barriers, by bringing people from different backgrounds on the same platform and giving them a dignified way of life.
Is Handloom same as Khadi?
A common question that comes to mind when we say “handloom” is What is the difference between Khadi and Handlooms? Are they same? There is a clear difference between the two.
To understand this, let’s examine the entire process of getting a fabric ready. It involves:
- Spinning the Yarn from raw cotton
- Processing and Dyeing the yarn
- Weaving the yarn into fabric
- Post processing like tailoring, ironing etc.
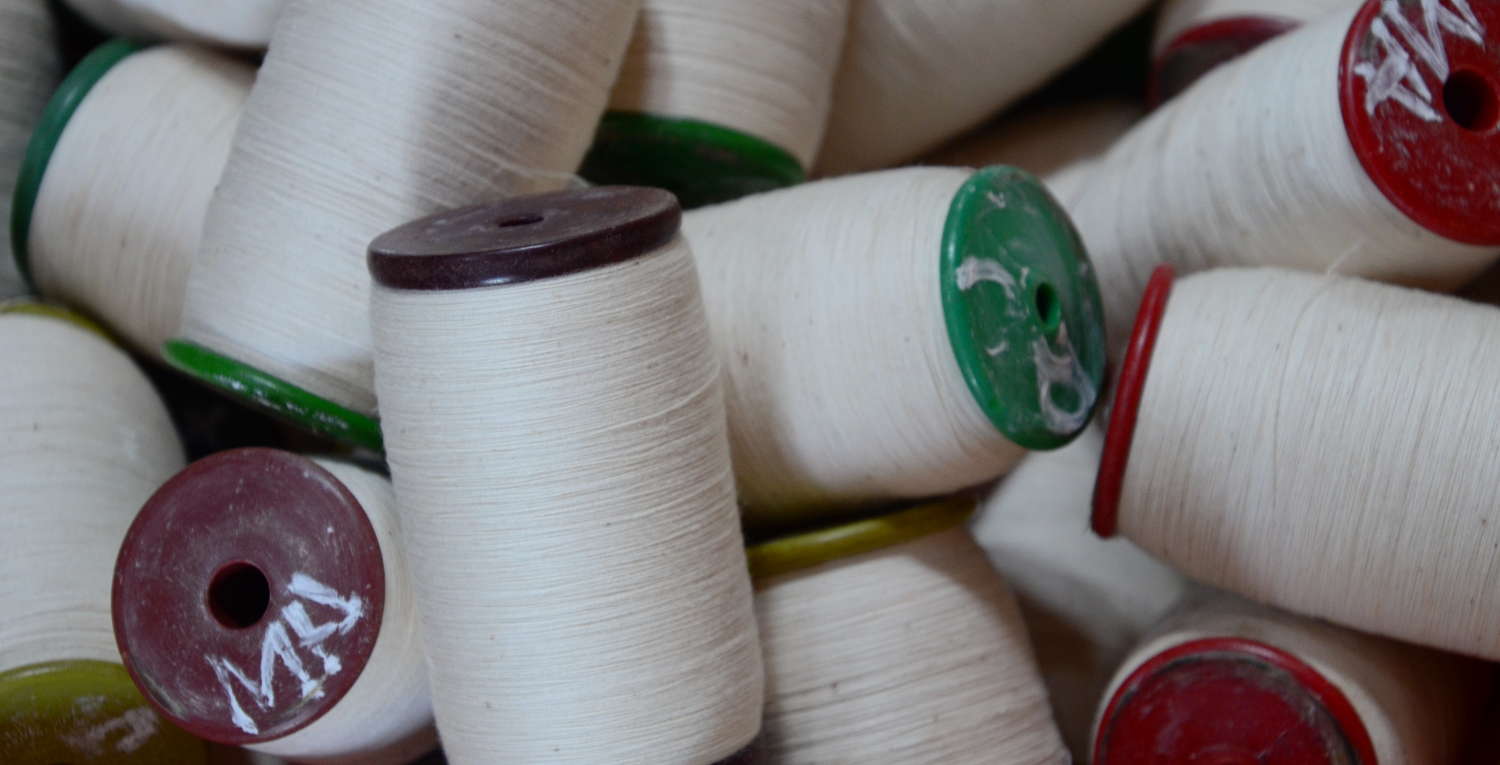
When a fabric is made entirely by hand, including spinning of yarn, it is called Khadi. When a fabric uses mill spun yarn, but uses all other processes by hand, it is called Handloom.
Handloom and Khadi are like cousins. The handloom weaver is common to both Khadi and Handloom.
Handloom Vs Powerloom
A power loom is a mechanized loom, and was one of the key developments in the industrialization of weaving during the early Industrial Revolution. The first power loom was designed in 1784 by Edmund Cartwright and first built in 1785. It is completely automatic, powered by electricity. A power loom requires lesser skill by weavers, as they only need to set the design and monitor the loom during operation. The introduction of power looms reduced the price of cloth in the market, giving rise to steep competition to handloom weavers.
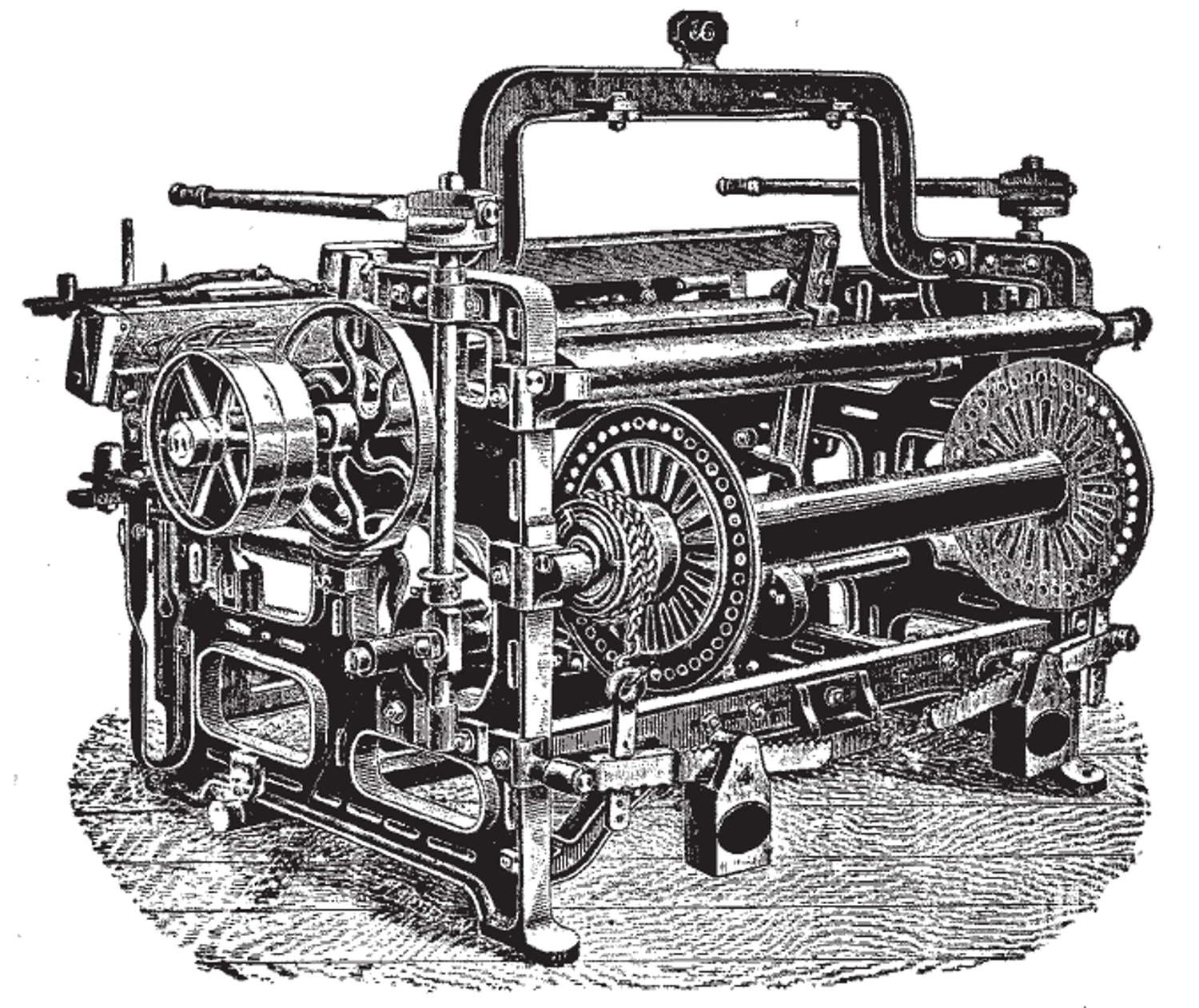
In a country like ours, where labour is available, where millions require employment, power looms have reduced the employment opportunities. A weaver can manage 3 powerlooms at a time, hence robbing several weavers of their livelihood. Wages are also reduced, leading to long working hours. Powerlooms run on electricity, hence are not as eco-friendly as handloom, which has a simpler setup and operation.
The cloth produced by power looms looks exactly like those produced by handlooms, and available at lesser cost. It is difficult to distinguish by just looking at the fabric.
Challenges facing Handloom
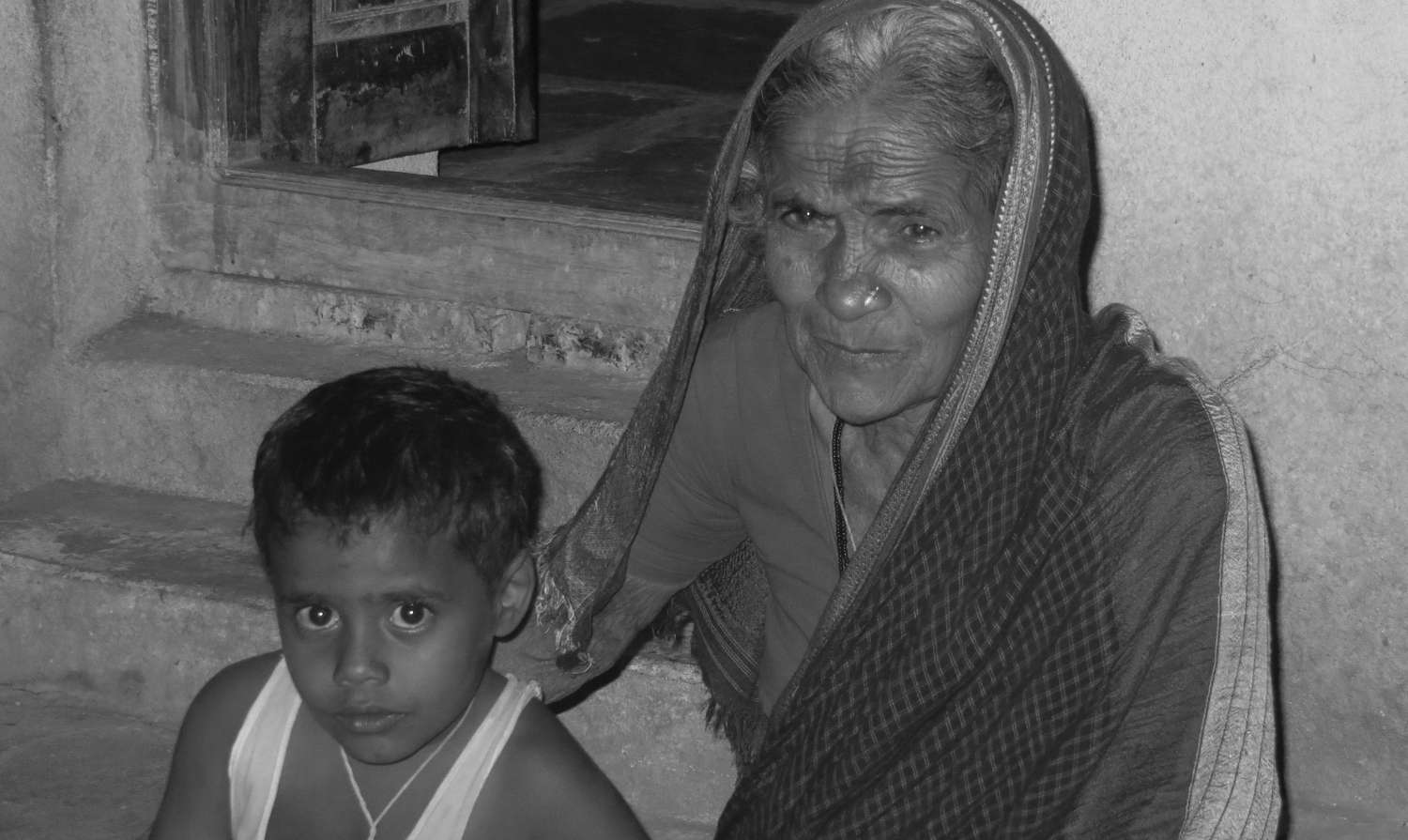
About 70% of the fabric being sold in the markets today as Handloom is actually powerloom fabric. Since it is not easy to find out, this leaves the consumers cheated. Also, it is one of the greatest threats faced by Handloom weavers as it eats away into their share of the market.
Government has a huge demand for cloth for their internal departments. State Govt itself requires 400 lakhs metres of cloth per year for their departments, this is procured largely from other parts of the country. The Govt. is not showing enough intent towards promoting the local tradition and utilizing local resources to meet the demands
People need to be made aware of the story behind handlooms. That it is not just a fabric and some designs, but a strong social statement, a way of life.
Due to lot of challenges and hardships faced by the traditional weaving families of handloom, the next generation is moving towards other professions resulting in loss of vital knowledge
Handloom Reservation Act
The handloom act of 1985 reserves some 11 variety of cloth to be woven exclusively as handloom. This ensured that there is a clear boundary for handloom and other fabric. However, the law is being violated by a few greedy traders who have been forcing powerloom weavers to weave these reserved fabric, resulting in the Handloom weavers left to fend for themselves.
Natural Dyeing of Yarn
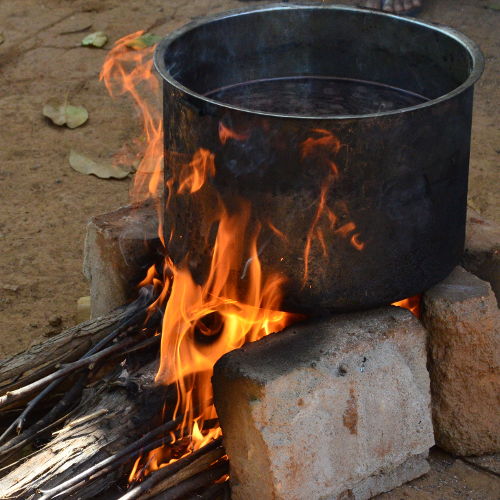
Scouring
Yarn procured is bound to have impurities, which have to be first removed before the dyeing process begins. This is part of the preparation of the yarn. A large tank of water is heated and the yarn is boiled in this water to remove oil and grime. This process is called scouring.
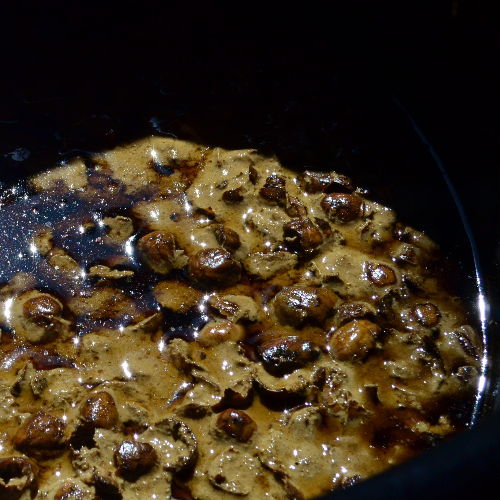
Hot Dyeing
The yarn is prepared by dipping it in a mordant solution. Alum is used as a mordant. This will aid for color fixing. The yarn is then dipped into the dye broth which is prepared according to the requirement. For getting mixture of colours, the yarn is dipped multiple times in different dye solutions. The second mordant dip, which is performed in the post treatment stage is done for specific dyes which require additional steps to ensure the right colour is obtained.
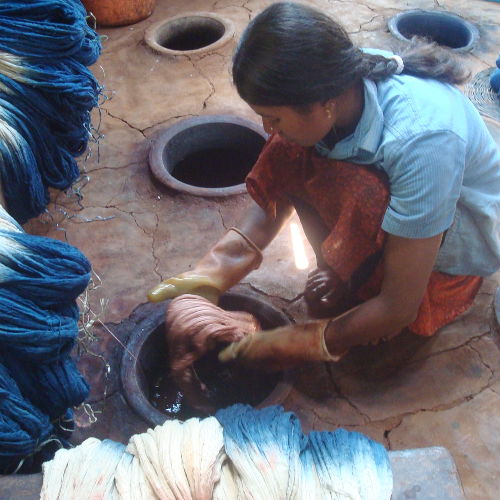
Cold Vat Dyeing
In this process of dyeing, the raw materials are mixed in a pot were it is left for 1-2 days to ferment. The yarn is dipped one or more times depending on the desired shade. Indigo is mixed in the vat along with limestone to obtain blue colour. 'Kasim Kari', where a concoction of jaggery, iron rust is left fermented for 15 days before using this to dip the yarn is used for black colour. The yarn, thus dyed is then dipped in a solution of myrobalan (alalekai). Areca peel is also prepared using the cold vat method of dyeing.
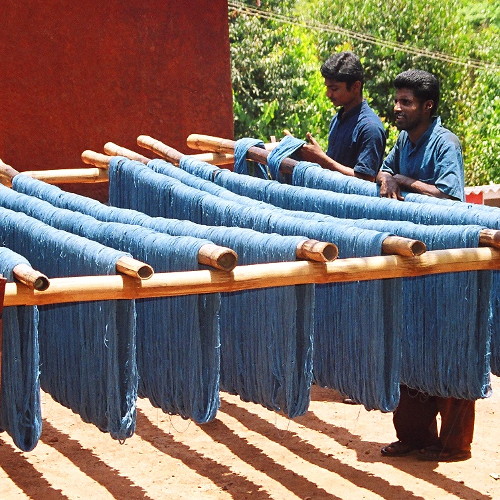
Drying
The dyed and treated yarn is then dried naturally and uniformly before sending to the weaving process.
Production of Fabric
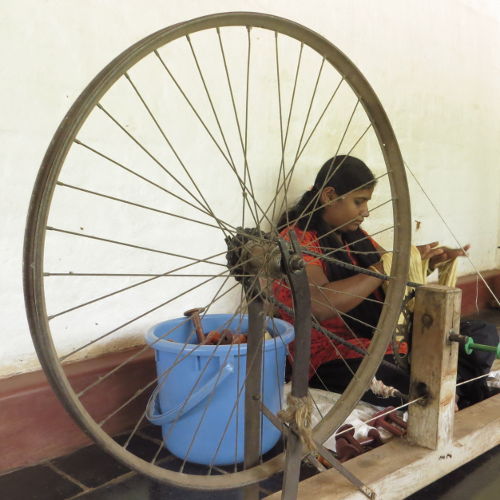
Pre-loom
The yarn (either unbleached 'kora' or dyed using natural dyes) is wound on bobbins of two different sizes - one used for the weft and the other for design setting for the warp. The bobbin is wound manually using a hand operated wheel. The bobbins of various colours are then loaded onto a design setting rack. Depending on the design of the warp, it is then fed into the loom to make a 'doli', which is then mounted onto the frame loom.
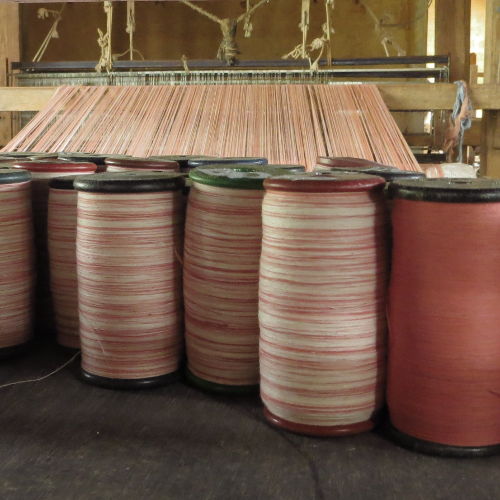
Loom
A hand operated wooden frame loom is used to weave the warp (doli that is loaded) and the weft to produce the desired patterns. Depending on the reed and pick of the fabric, the resultant fabric strength, density is controlled. A frame loom can produce about 240 metres of fabric with one 'doli' or bundle. Depending on specific designs, some additions, called 'dobby' can be made to the loom to create the desired patterns.
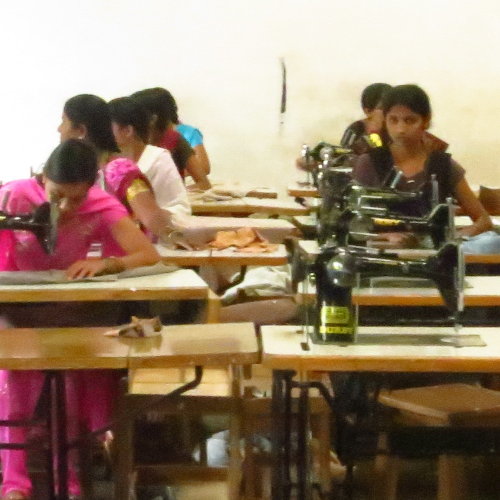
Post-loom
The post loom processes vary depending on the intended garment or finished product like stitching, block printing, Embroidery (Kasuthi), Tie-dyeing, Shrinking and Ironing.